McKinsey’s Roland Rechtsteiner on the energy transition and commodities markets
Inextricably connected to transitioning energy markets, commodities markets will remain volatile – and could be a "catalyst" for change, says McKinsey's Roland Rechtsteiner.
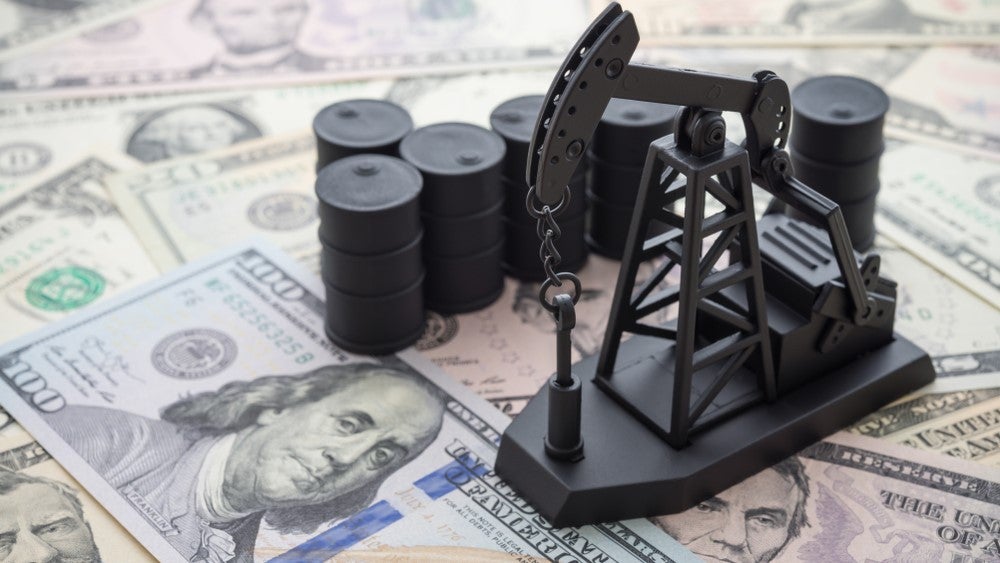
US increases royalty rates for companies drilling on public lands
‘Sheer scale of the challenge’ the biggest barrier to net zero in APAC
Venezuela’s former oil minister arrested for money laundering
How “energy-hungry AI” is straining grids and spreading climate disinfo