UK’s NSTA awards 31 new North Sea oil and gas exploration licences
The new licences are estimated to contribute approximately 600 mmboe by 2060.
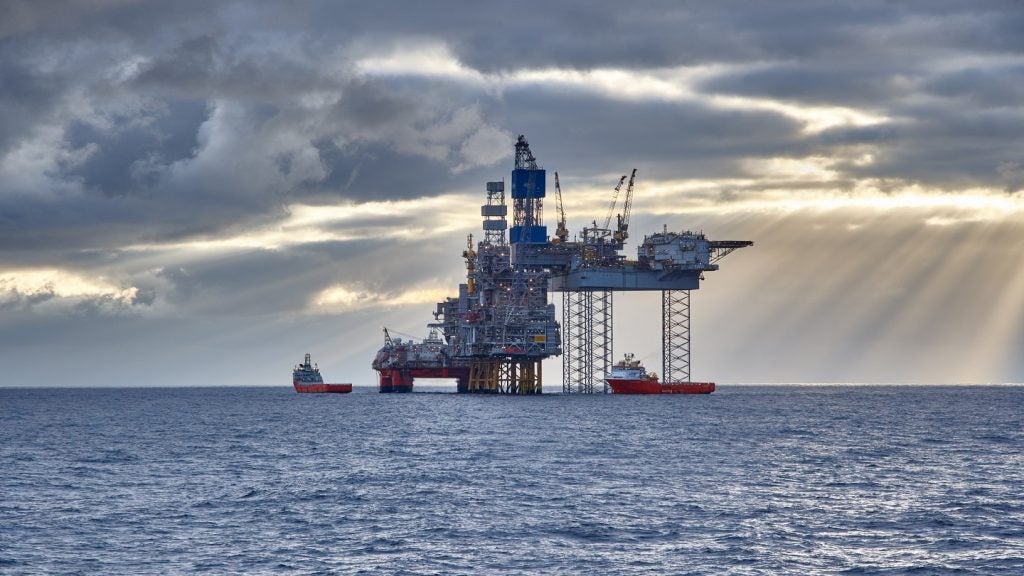
The new licences are estimated to contribute approximately 600 mmboe by 2060.
The deal will see Presight acquire a 51% stake in AIQ, an AI company focused on developing solutions for the oil and gas industry.
The oil & gas industry continues to be a hotbed of patent innovation. Activity is driven by the need for...
Thailand’s anti-corruption authority finds former PTTEP executives guilty
How residential PV storage is paving the way for net-zero living
How residential PV storage is paving the way for net-zero living
“A bumpy ride” for cybersecurity as AI poses new threats – GlobalData report